VE全国大会が開かれました。
期日:11月16日(火)〜17日(水)
会場:アルカディア市谷。
参加者:2日間延べ1000名を越した。(近年にない盛況でした)
講演では
1.「トヨタ生産方式の本質と進化/深化」:トヨタ 林南八技監
ナンパチ先生で有名な、大野耐一先生の愛弟子。ズバリズバリきました。感動でした。トヨタのモノ作りの秘伝を我々に力強く示唆してくださいました。語録の中から抜粋すると、
* ニンベンの付く「自働化」:異常があれば止まる。人は機械の番人であってはならない
* Just in Time:必要なものを必要な時に必要なだけ造る。
* リードタイム:行動を興した時(受注とか)から完成・納入までの期間を指し、短縮ニーズは資金回収である事。
* お客様第一主義:良いものを・早く・タイムリーにお届けする。
* 日本の製造業は競争力を失うわないためには:基本を失うな、過大投資をするな
* 内製化を進めよ
* 売れるペースで造れ:早く作ることも必要だが造りすぎると停滞を呼ぶ。
* リードタイムが短縮できると平準化が進む。製品で持つから倉庫が必要になる。情報で盛っていたら倉庫は要らない。
* リードタイム:一番時間の掛かるものからスタート。内部の事情などお客様は知らぬ。
* 見える現場:結果管理でなく、今の「正常・異常管理」
* 5回のなぜ?:多くは頭で考える。これは禁物。現場現物でなぜ?を5回繰り返せ。
* 改善を継続する秘訣はトップが現場に出て事実に直面する事だ。
* スローガンやキャッチフレーズでは人は動かない。数値目標にすること。
* 原価低減は生産性がキー:労働生産性、設備生産性、材料生産性
* 中国に勝つにはオンリーワン技術の確立だ:そのためには井の中の蛙になるな、限りなく内製化をせよ。
歴代のトヨタ幹部の言葉も感動でした。ナンパチ先生ありがとうございました。
2.「日産リバイバルプラン成功の秘訣」日産 増田本部長
* 何が低迷の原因になったか(ゴーン氏来日3ヶ月の印象)
@ クリアな利益思考の欠如
A 顧客に対する商店が不十分
B クロスファンクショナルで、クロスボーダーな業務の欠如
C 危機感の欠如
D 共通のビジョンや共通の長期計画の欠如
* 3−3−3とは
@ 「サプライヤー」「日産購買」「日産技術開発」のトライアングル
A 「日本・アジア」「米州」「欧州・中近東・アフリカ」地域のトライアングル
B 3年間の取り組み(NRPは結果2年で△20%原低、NISSAN180は02年から
3年間で15%の原低。
* キーワード:CQDとスピード
* 原価低減活動
@
部品の仕様変更、材料の変更
A
検査基準の見直し
B
目標性能、装備、バリエーションの見直し
C
モジュール化
D
部品共通化、種類数の削減
* 原価低減推進のコンセプト:Design to Cost ⇒ CQD
* 事例:ネスティング。集中CR(開発を1ヶ月止めた。3−3−3エンジニアと購買の大部屋化。テアダウン。開発プロセスの改善。その他。
印象:再建時のセオリーでした。いすゞで関和平(社長)と我々が取り組んだ事、マツダでヘンリー
ウォレスが行った事、幾多の再建企業の軌跡と全く変わらず内容への感動は薄かった。印象はゴーンの指導力、系列破壊や工場売却による危機感の扇動、強烈な数値管理などにあった。ちなみに佐藤の山梨の山荘に日産の人たちが毎年集う。彼らはゴーンの呼び方をゴーンが来た頃には「ゴーンちゃん」→「ゴーンのやつ」→「ゴーン」→「ゴーンさん」と変化してきた事が今思い出される。関社長(いすゞ)にしかり、やはり改革には強力な指導者と指導力が必要だとの実感。
そのほかに
* コーチトウェンティワンの桜井副社長の「結果を出す部下を作るコーチング術」
* 元常総学園野球部監督木内幸男氏「木内流=勝つ組織=の作り方」
* 日立製作所ソリューションズベンチャーカンパニーCEO井村 亮氏「超小型ICタグ・ミューチップの可能性と今後の展開」
* 等の講演、いずれも久々に佐藤は聞き入りました。
その他、発表多数(論文、事例)
中でも佐藤の親友(今秋、アメリカでテアダウンの本を共著・発行)Jerry Kaufman氏がFAST Modelを用いた各種プロセスへのアプローチ事例は、と核問題をあいまいにしがちなアプローチにおいて、FAST(機能系統図…日本の物とは幾分異なる)を用いる事で各プロセスの問題の大きさ把握や創造性の発揮に貢献できるVEの基本中の基本を暑く発表してくれた。とかく海外の発表は換算とするがさすが第一人者。多くのVErを惹きつけた。
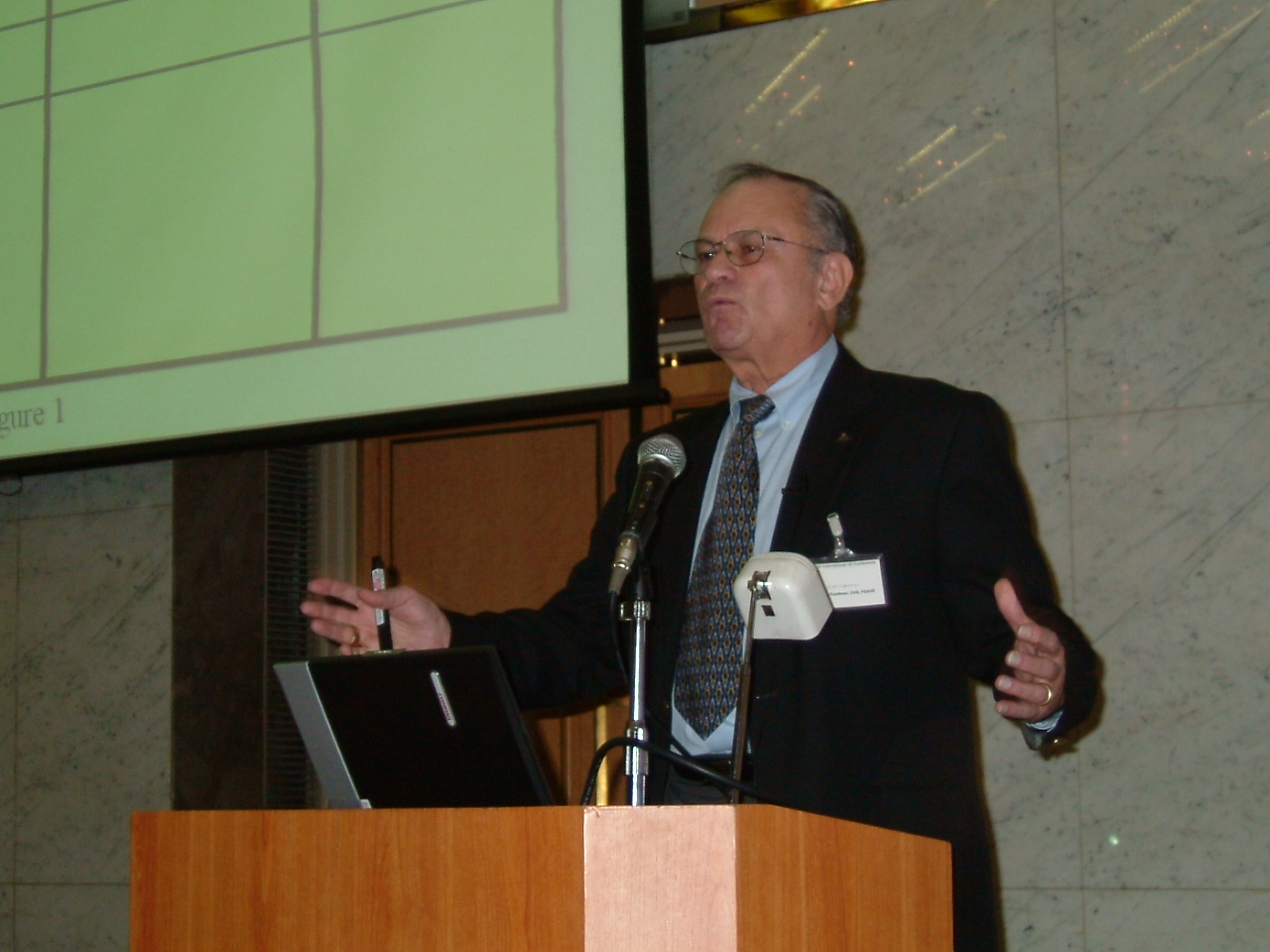
2005年は名古屋で9月7・8日です。
愛知万博を兼ねて皆で行きましょう。
詳しくはVE協会のホームページ http://www.sjve.org/ をご覧ください。

